1. Historia Rozwoju Obrabiarek CNC
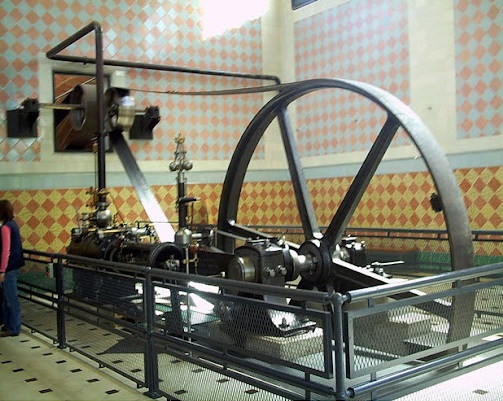
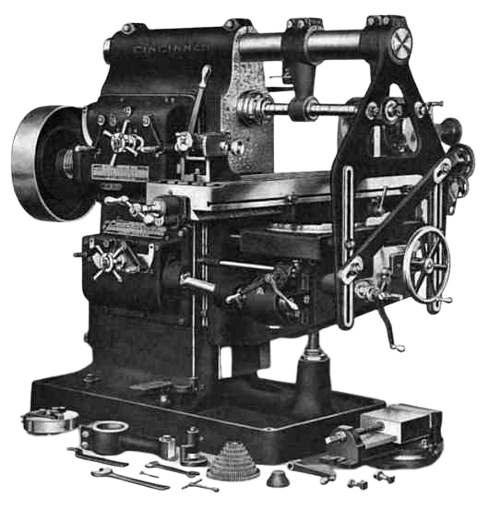
- Lata 50. XX wieku: Początki sterowania numerycznego (NC)
-
W latach 40. i 50. XX wieku John T. Parsons wraz z Richardem J. Kegg zainicjowali rozwój
sterowania
numerycznego (NC). Badania były finansowane przez siły powietrzne Stanów Zjednoczonych, które
potrzebowały narzędzi do produkcji skomplikowanych części lotniczych.
MIT Servo Mechanisms Laboratory odegrało kluczową rolę w rozwoju pierwszego systemu NC, który korzystał z taśm perforowanych do kontrolowania ruchu maszyny.
Pierwsze maszyny NC bazowały na modyfikacji istniejących maszyn konwencjonalnych, wyposażonych w silniki krokowe i układy sterujące.
- Ewolucja CNC: Od taśm perforowanych do komputerowego sterowania numerycznego
Taśmy perforowane: Na początku dane dla maszyny były zapisane na taśmach z otworami, które kodowały ruchy osi i funkcje maszyny. Był to pierwszy krok ku automatyzacji, ale system był wolny i podatny na błędy mechaniczne.
Pojawienie się mikroprocesorów (lata 70.): Zastąpienie taśm komputerami pozwoliło na dynamiczne wprowadzanie danych oraz przechowywanie programów na nośnikach cyfrowych.
Rozwój CNC: Dzięki integracji sterowników komputerowych system CNC (Computer Numerical Control) znacznie zwiększył dokładność, elastyczność i efektywność maszyn.
- Wprowadzenie systemów CAD/CAM i ich integracja z obrabiarkami CNC
Systemy CAD (Computer-Aided Design) umożliwiają projektowanie modeli 2D i 3D, które są następnie przekształcane w kod CNC za pomocą CAM (Computer-Aided Manufacturing).
Integracja tych systemów z maszynami CNC przyspieszyła proces produkcji, minimalizując czas potrzebny na przejście od projektu do gotowego detalu.
Ciekawostka: CAD/CAM wprowadziły automatyczną optymalizację procesów obróbczych, redukując marnotrawstwo materiału.
- Pierwsze zastosowanie CNC w lotnictwie
Branża lotnicza była pionierem w wykorzystaniu CNC. Skomplikowane kształty części silników i skrzydeł wymagały precyzji, której nie mogły zapewnić konwencjonalne maszyny.
Przykład: North American Aviation wykorzystało system CNC do produkcji części dla samolotu F-86 Sabre, co stało się milowym krokiem w rozwoju technologii.
Efekt: Redukcja czasu produkcji i wzrost jakości części lotniczych sprawiły, że CNC zyskało popularność w wielu innych branżach, takich jak motoryzacja i elektronika.
2. Definicja Obrabiarki CNC
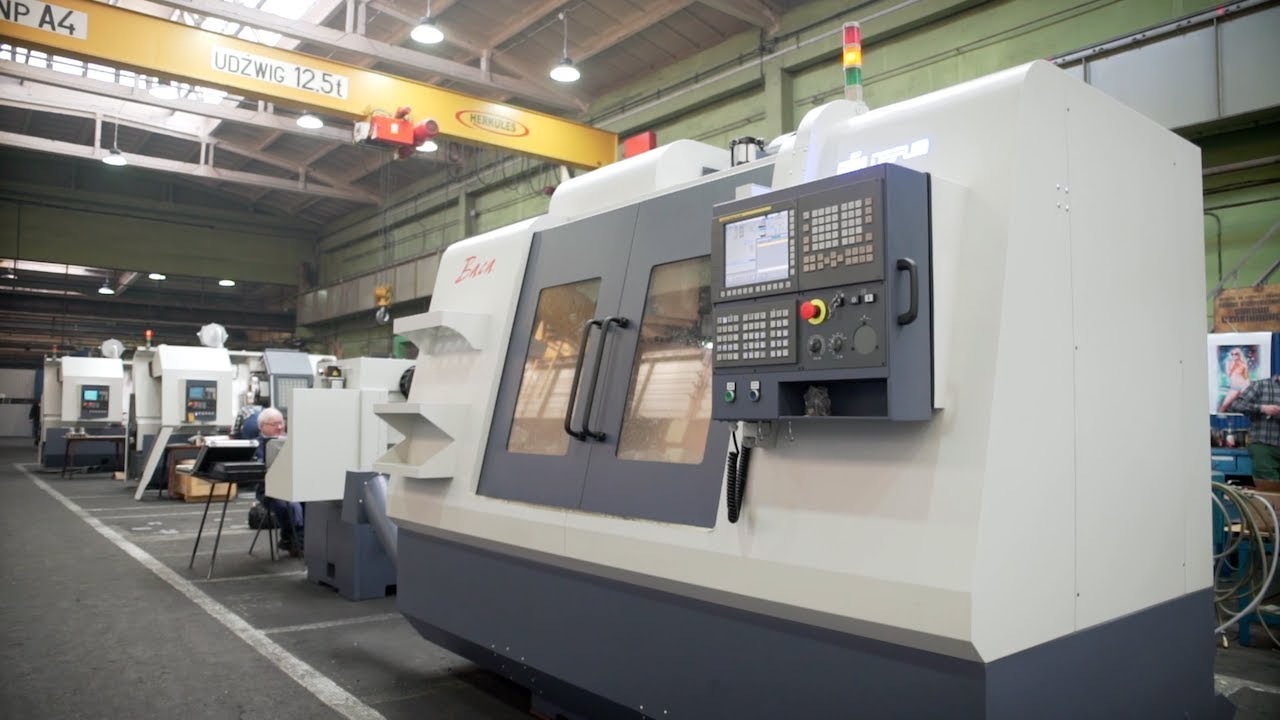
Obrabiarka CNC (Computer Numerical Control) to maszyna skrawająca wyposażona w komputerowe sterowanie, umożliwiające precyzyjną, zautomatyzowaną i powtarzalną obróbkę różnorodnych materiałów, takich jak metale, tworzywa sztuczne czy drewno. Dzięki zastosowaniu sterowania numerycznego maszyna realizuje zaprogramowane ścieżki ruchu narzędzia względem obrabianego materiału.
- Cechy charakterystyczne:
Możliwość tworzenia złożonych kształtów przy minimalnym udziale operatora.
Wysoka dokładność rzędu 0,001 mm.
Powtarzalność procesu niezależnie od liczby produkowanych elementów.
- Porównanie z Maszynami Konwencjonalnymi
CNC
Konwencjonalna
- Automatyzacja:
- Pełna automatyzacja procesu, od ustawienia narzędzia po realizację operacji.
- Wymagają manualnej obsługi i nadzoru operatora.
- Dokładność:
- Precyzyjne sterowanie i kompensacja błędów.
- Zależne od umiejętności operatora.
- Złożoność:
- Obsługa za pomocą G-kodów, możliwe programowanie zaawansowanych ścieżek narzędzia.
- Ograniczone do prostych ruchów i kształtów.
- Elastyczność:
- Łatwość modyfikacji programu dla różnych detali.
- Konieczność manualnego dostosowania maszyny.
- Automatyzacja:
- Zastosowania Obrabiarek CNC
Lotnictwo
Przemysł samochodowy
- Przemysł lotniczy:
Produkcja skomplikowanych części silników odrzutowych i elementów strukturalnych.
Obróbka lekkich i wytrzymałych materiałów, takich jak tytan i kompozyty.
- Przemysł samochodowy:
Toczenie części silników, produkcja przekładni, elementów zawieszenia.
Obróbka precyzyjna dla masowej produkcji.
- Przemysł medyczny:
Wytwarzanie implantów ortopedycznych i dentystycznych.
Precyzyjna obróbka materiałów biokompatybilnych.
- Przemysł elektroniczny:
Frezowanie płytek drukowanych (PCB) i obudów urządzeń elektronicznych.
Wycinanie otworów w komponentach precyzyjnych.
- Produkcja masowa i jednostkowa:
Masowa produkcja części zamiennych i akcesoriów.
Jednostkowa produkcja prototypów w procesach badawczo-rozwojowych.
Przemysł medyczny
Produkcja masowa
- Przemysł lotniczy:
3. Budowa i Charakterystyka Obrabiarek CNC
Podstawowe elementy obrabiarek CNC:
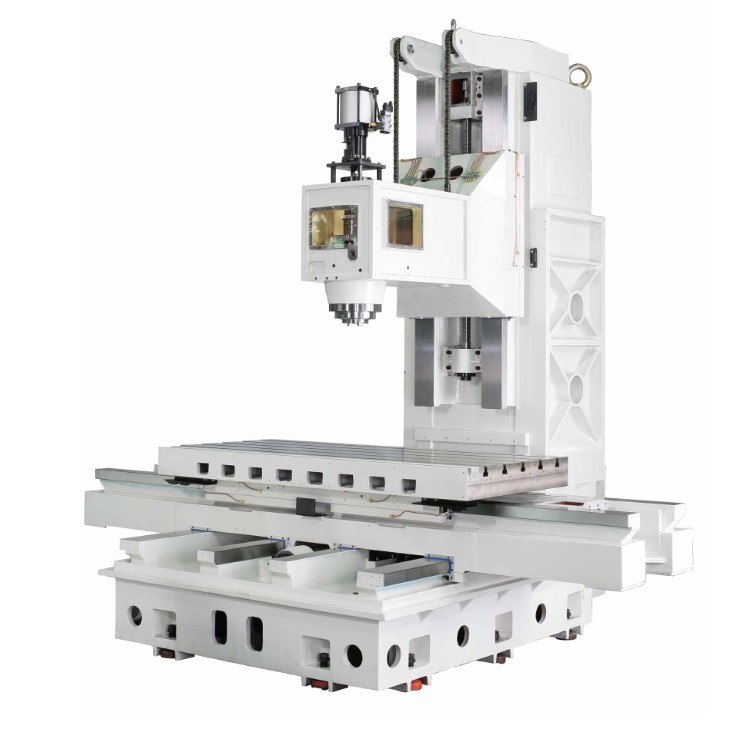
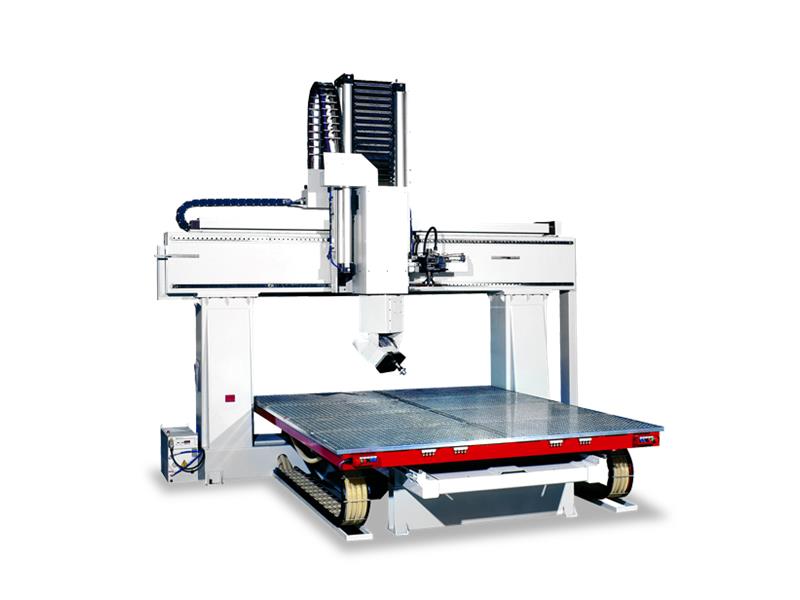
-
Korpus
- Korpus obrabiarki CNC to sztywna i wytrzymała konstrukcja, której głównym zadaniem jest zapewnienie stabilności maszyny podczas pracy. Jest to fundament całej maszyny, który wpływa na jej dokładność i precyzję obróbki. Korpus wykonany jest z materiałów o dużej sztywności, takich jak stal, żeliwo lub kompozyty, aby zminimalizować wibracje i zniekształcenia podczas obróbki. Bez odpowiedniej sztywności konstrukcji, maszyna może nie osiągać wymaganej precyzji.
-
Osie Robocze
-
Obrabiarki CNC zazwyczaj mają od 3 do 5 osi roboczych, które pozwalają na wykonywanie
skomplikowanych operacji obróbczych w różnych kierunkach.
3-osie: Standardowe obrabiarki, w których narzędzie porusza się wzdłuż trzech osi – X (poziomo), Y (pionowo), Z (głębokość).
5-osie: Bardziej zaawansowane maszyny, które umożliwiają dodatkowe ruchy wokół osi X, Y, Z, co pozwala na obróbkę bardziej skomplikowanych detali, np. obrabianie części o dużych kątach lub krzywiznach. Dzięki temu maszyna CNC staje się bardziej elastyczna i zdolna do pracy z bardziej złożonymi elementami.
-
Napędy
-
Obrabiarki CNC wykorzystują różne typy napędów, najczęściej serwosilniki i silniki krokowe,
z których każdy ma swoje zalety i wady.
Serwosilniki: Są to silniki, które oferują bardzo wysoką precyzję i wydajność. Pracują w zamkniętej pętli sprzężenia zwrotnego, co oznacza, że są w stanie monitorować i korygować swoje położenie. Zapewniają dużą moc i dokładność, ale są droższe i bardziej skomplikowane w implementacji.
Silniki krokowe: Wykorzystywane głównie w prostszych systemach CNC. Charakteryzują się mniej skomplikowaną konstrukcją i niższymi kosztami, ale oferują niższą dokładność i prędkość w porównaniu do serwosilników. Silniki krokowe są idealne do zastosowań, w których precyzja nie jest kluczowa, a koszt jest czynnikiem decydującym.
-
System Sterowania
Komputer: Komputer jest centralnym układem sterującym w nowoczesnych obrabiarkach CNC. Odpowiada za przetwarzanie danych wejściowych (np. G-kodów) i przekazywanie ich do napędów maszyny, co pozwala na realizację złożonych operacji obróbczych.
Sterownik PLC (Programmable Logic Controller): PLC to specjalistyczny system sterowania, który może współpracować z komputerem lub działać samodzielnie w mniej zaawansowanych maszynach. Jego głównym zadaniem jest kontrolowanie podstawowych funkcji maszyny, takich jak napędy, chłodzenie czy zmiana narzędzi. Zaletą PLC jest niezawodność i łatwość w integracji z innymi systemami przemysłowymi.
-
Chłodzenie
-
Chłodzenie w obrabiarkach CNC jest niezwykle ważne dla zachowania precyzyjności oraz
wydłużenia żywotności narzędzi skrawających. Wysoka temperatura generowana podczas obróbki
może prowadzić do przegrzania, co może wpłynąć na jakość wykonania detali.
Chłodzenie cieczą: Wykorzystuje się specjalne płyny chłodzące (np. oleje lub emulsje wodne), które są kierowane na miejsce skrawania, aby chłodzić narzędzie i materiał. Dodatkowo, takie płyny pomagają w usuwaniu wiórów.
Chłodzenie powietrzem: W prostszych obrabiarkach, gdzie skrawanie nie generuje dużych ilości ciepła, stosuje się chłodzenie powietrzem. Jest to mniej efektywna metoda, ale tańsza i wystarczająca w przypadku mniej wymagających operacji obróbczych.
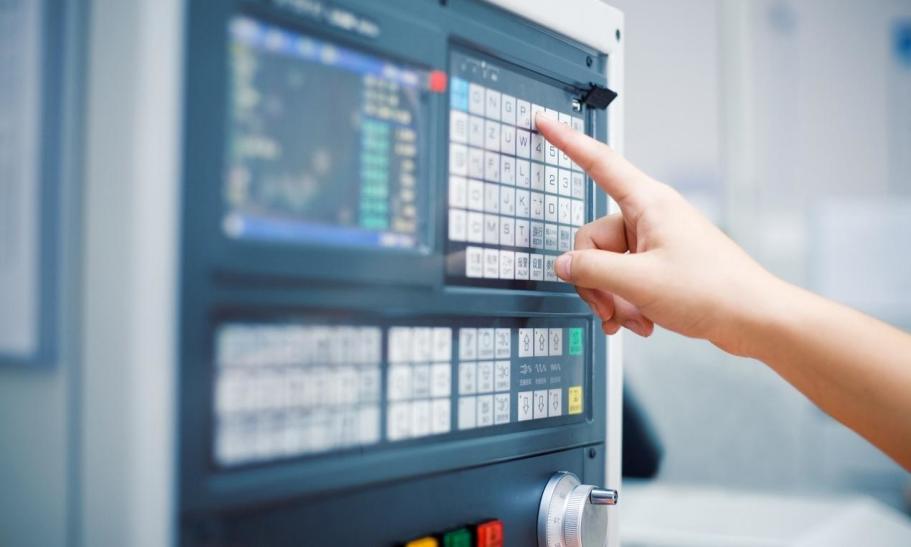
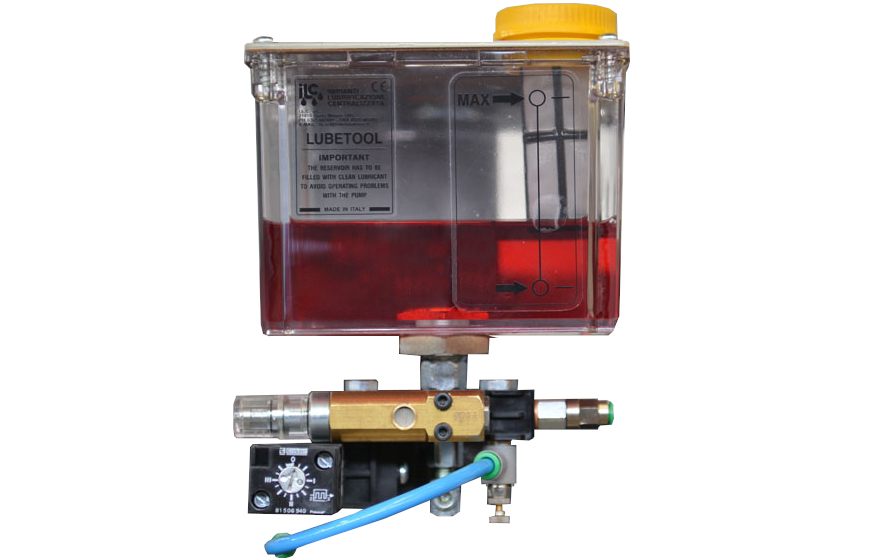
3. Rodzaje narzędzi stosowanych w obrabiarkach CNC
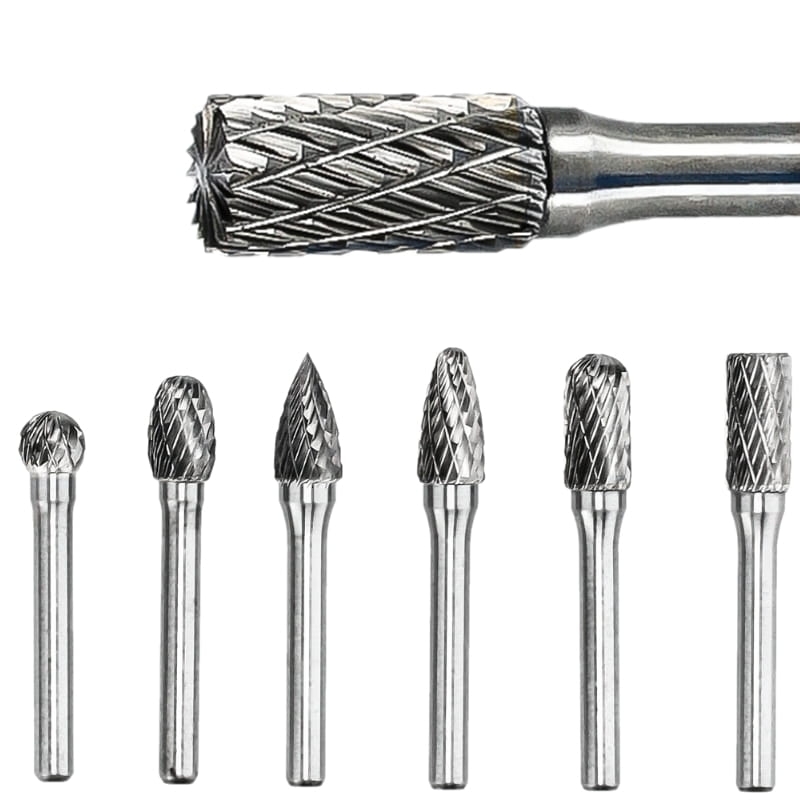
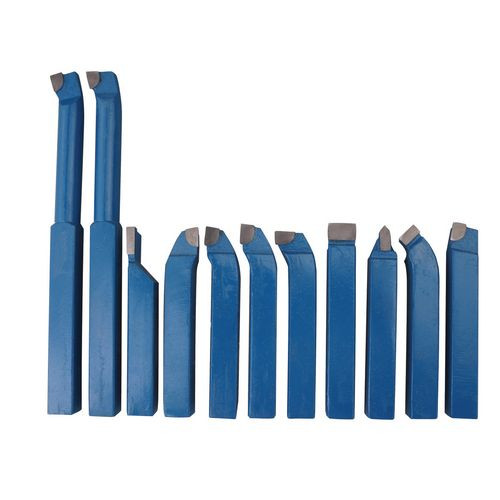
-
Frezy
-
Frezy są jednym z najczęściej używanych narzędzi skrawających w obrabiarkach CNC,
przeznaczonymi do obróbki materiałów poprzez skrawanie. W zależności od kształtu i
zastosowania, wyróżnia się kilka rodzajów frezów:
Frezy walcowe: Narzędzia o cylindrycznym kształcie, wykorzystywane głównie do frezowania płaskich powierzchni oraz do wykonywania rowków i wpustów.
Frezy kulowe: Posiadają kulistą końcówkę i są wykorzystywane do obróbki kształtów o dużych krzywiznach oraz w procesach, gdzie wymagana jest precyzyjna obróbka w trzech wymiarach (np. formy wtryskowe).
Frezy tarczowe: Używane do cięcia wzdłużnego i poprzecznego w materiałach o większej grubości. Dzięki swojej konstrukcji umożliwiają obróbkę szerszych powierzchni w jednym przejściu.
-
Noże Tokarskie
-
Noże tokarskie są narzędziami wykorzystywanymi w tokarkach CNC, służącymi do skrawania
materiałów cylindrycznych i stożkowych. W zależności od konstrukcji i zastosowania, dzielą
się na:
Noże tokarskie stałe: Mają jedną stałą krawędź skrawającą i są stosowane głównie w przypadku prostych operacji skrawających.
Noże z wymiennymi płytkami skrawającymi: Wymienne wkładki pozwalają na łatwą wymianę uszkodzonych części narzędzia, co zwiększa ekonomiczność i wydajność produkcji. Płytki te są często wykonane z materiałów o wysokiej twardości, takich jak węgliki spiekane.
-
Wiertła i Rozwiertaki
-
Wiertła i rozwiertaki są stosowane w obrabiarkach CNC do wykonywania otworów o różnych
średnicach i precyzji.
Wiertła: Narzędzia o stożkowym kształcie, przeznaczone do wykonywania otworów w materiałach. Wiertła mogą mieć różne średnice i są stosowane do wiercenia otworów o średnicy od kilku milimetrów do kilku centymetrów.
Rozwiertaki: Narzędzia wykorzystywane do wykańczania otworów i poprawy ich dokładności wymiarowej oraz jakości powierzchni. Zwykle używane po wiertłach w celu osiągnięcia większej precyzji.
-
Materiały Narzędzi
-
Narzędzia skrawające muszą charakteryzować się wysoką twardością, odpornością na zużycie
oraz odpornością na wysokie temperatury, co umożliwia im skuteczną obróbkę trudnych
materiałów. W zależności od potrzeb, narzędzia skrawające wykonuje się z różnych materiałów:
Stal szybkotnąca (HSS): Jest to stop węgla i innych metali, wykorzystywany w narzędziach, które muszą pracować w wysokiej temperaturze. HSS cechuje się dobrą odpornością na ścieranie oraz zdolnością do pracy w wysokich temperaturach, ale ma mniejszą twardość niż inne materiały, takie jak węgliki spiekane.
Węgliki spiekane: Stosowane w narzędziach skrawających do obróbki twardych materiałów, takich jak stal nierdzewna czy tytan. Charakteryzują się dużą twardością, odpornością na wysokie temperatury oraz bardzo dobrą trwałością, jednak są mniej odporne na uderzenia.
Ceramika: Wykorzystywana w narzędziach do obróbki twardych materiałów. Ceramika charakteryzuje się wyjątkową twardością oraz odpornością na ścieranie, ale jest bardziej krucha i podatna na pęknięcia przy dużych obciążeniach mechanicznych.
Diament: Najtwardszy znany materiał, stosowany w narzędziach do obróbki bardzo twardych materiałów. Narzędzia diamentowe są wykorzystywane m.in. w precyzyjnej obróbce metali, materiałów kompozytowych czy kamieni szlachetnych.
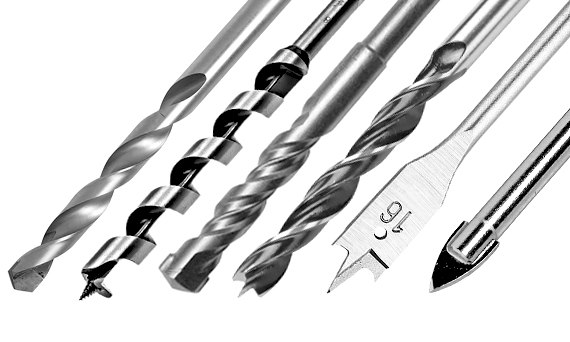
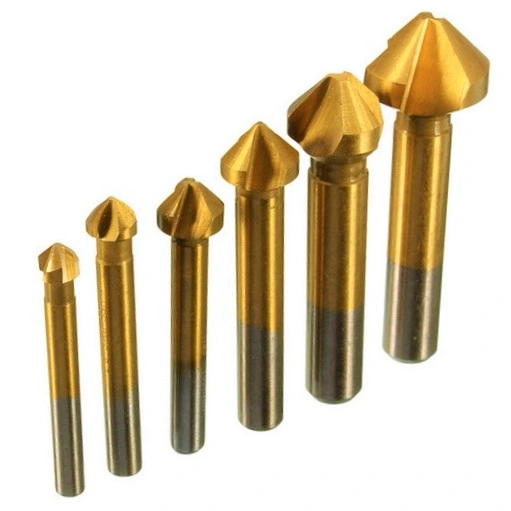
4. Parametry techniczne obrabiarek:
-
Prędkość obrotowa wrzeciona
-
Prędkość obrotowa wrzeciona odnosi się do liczby obrotów, jakie wrzeciono może wykonać w
ciągu jednej minuty (RPM – obroty na minutę). Jest to kluczowy parametr, który determinuje
szybkość skrawania i rodzaj materiału, który można obrabiać.
Zakres prędkości: W zależności od typu maszyny, prędkość obrotowa wrzeciona może wynosić od kilku tysięcy do nawet 30 000 RPM. Wyższe prędkości obrotowe są często stosowane w obrabiarkach do precyzyjnych operacji, takich jak frezowanie detali o bardzo małych wymiarach czy obróbka materiałów takich jak aluminium, mosiądz czy tworzywa sztuczne. Przykład: Frezy kulowe w obrabiarkach CNC mogą pracować z prędkościami do 20 000-30 000 RPM, aby uzyskać gładkie i precyzyjne wykończenie.
-
Dokładność
-
Dokładność obrabiarki CNC określa, jak małe mogą być odchyłki wymiarowe od zaplanowanego
kształtu detalu. Tolerancje są wyrażane w mikrometrach i zależą od typu maszyny oraz
zastosowanego narzędzia.
Typowa dokładność: Dla wielu maszyn CNC tolerancje mogą wynosić ±0.002 mm, co oznacza, że detal może mieć wymiary różniące się od zaplanowanego o nie więcej niż 2 mikrometry. W bardziej precyzyjnych maszynach, takich jak frezarki 5-osiowe, dokładność może wynosić ±0.001 mm.
Zdolność do zachowania bardzo małych tolerancji jest kluczowa w takich branżach jak przemysł lotniczy, medyczny czy elektroniczny, gdzie precyzyjne dopasowanie części ma kluczowe znaczenie.
-
Przebieg osi
-
Przebieg osi to zakres ruchu wzdłuż osi roboczych maszyny, który decyduje o maksymalnych
wymiarach detali, jakie mogą być obrabiane.
Typowe wartości:
- Oś X: Zwykle wynosi 1000 mm (ruch w poziomie).
- Oś Y: Zwykle wynosi 500 mm (ruch w kierunku poprzecznym).
- Oś Z: Zwykle wynosi 500 mm (ruch w kierunku pionowym).
5-osiowe maszyny CNC mogą mieć bardziej rozbudowane zakresy, umożliwiające obróbkę większych i bardziej złożonych detali.
Zastosowanie: Większy przebieg osi pozwala na obróbkę większych elementów, a także na skomplikowane operacje, jak np. obróbka detali w różnych pozycjach.
-
Maksymalne obciążenie stołu roboczego
-
Maksymalne obciążenie stołu roboczego określa, ile materiału lub detali może być
jednocześnie obrabianych na stole maszyny, nie przekraczając dopuszczalnego nacisku, co może
wpłynąć na stabilność i precyzję operacji.
Typowe wartości: Maksymalne obciążenie stołu roboczego w wielu obrabiarkach CNC wynosi 300 kg.
W bardziej zaawansowanych maszynach przemysłowych obciążenie to może być większe, sięgając nawet 1000 kg w przypadku dużych obrabiarek, takich jak tokarki CNC do obróbki dużych detali przemysłowych.
Wartość ta ma wpływ na dobór maszyny do zastosowań – w przypadku ciężkich materiałów, takich jak stal, należy wybierać maszyny o wyższym dopuszczalnym obciążeniu.
5. Charakterystyka wybranych typów obrabiarek
-
Frezarki CNC
-
Frezarki CNC są maszynami, które wykorzystują narzędzia skrawające – frezy – do obróbki
materiałów. Mogą być wykorzystywane do obróbki powierzchni płaskich, konturowych oraz
skomplikowanych, trójwymiarowych kształtów. Dzięki możliwości pracy w wielu osiach, frezarki
CNC potrafią obrabiać zarówno detale o skomplikowanych kształtach, jak i precyzyjnie
obrabiać dużą powierzchnię.
Zastosowanie: Frezarki CNC są stosowane w wielu branżach, takich jak przemysł lotniczy, motoryzacyjny, elektronika, przemysł spożywczy czy medyczny. Używa się ich m.in. do obróbki form wtryskowych, produkcji narzędzi skrawających, produkcji części maszyn i urządzeń.
Rodzaje frezów: Frezarki CNC mogą wykorzystywać różne typy frezów (walcowe, kulowe, tarczowe), co pozwala na obróbkę materiałów o różnych właściwościach. Możliwość regulacji prędkości wrzeciona oraz zmiennej geometrii narzędzia pozwala na optymalizację procesu skrawania w zależności od rodzaju materiału.
-
Tokarki CNC
-
Tokarki CNC to maszyny służące do obróbki materiałów w formie brył obrotowych (np. wałków,
cylindrów, stożków). Są to jedne z najstarszych typów obrabiarek CNC, wykorzystywane głównie
do skrawania przedmiotów o okrągłym przekroju, takich jak wały, tuleje czy pierścienie.
Zasada działania: W tokarkach CNC materiał jest obracany wokół osi, a narzędzie skrawające porusza się wzdłuż tej osi, wykonując cięcie. Dzięki temu możliwe jest uzyskanie bardzo precyzyjnych detali o okrągłych kształtach.
Zastosowanie: Tokarki CNC znajdują szerokie zastosowanie w produkcji detali takich jak elementy silników, przekładni, wały, tuleje, elementy do przemysłu motoryzacyjnego, lotniczego czy energetycznego.
-
Elektrodrążarki
-
Elektrodrążarki to maszyny wykorzystywane do obróbki wyładowaniami elektrycznymi (EDM –
Electric Discharge Machining). Proces ten polega na wykorzystaniu serii wyładowań
elektrycznych pomiędzy elektrodą a obrabianym materiałem, co prowadzi do stopniowego
wypalania materiału.
Zastosowanie: Elektrodrążarki są szczególnie przydatne do obróbki bardzo twardych materiałów, które są trudne do obróbki tradycyjnymi metodami skrawania. Stosowane są do produkcji narzędzi, form wtryskowych, matryc, a także do obróbki detali o skomplikowanych kształtach, które nie mogą być łatwo wycięte przy użyciu tradycyjnych narzędzi skrawających.
Rodzaje:
- Elektrodrążarki drutowe: Używają cienkiego drutu, który porusza się wzdłuż obrabianego materiału, wykonując precyzyjne cięcia.
- Elektrodrążarki wgłębne: Używają elektrod, które wtłaczane są w materiał, aby wykonać drążenie w detalu.
-
Ploter Laserowy
-
Plotery laserowe to maszyny CNC, które wykorzystują technologię lasera do cięcia i
grawerowania materiałów. Strumień lasera działa na materiał, pod wpływem którego następuje
jego topnienie, wypalenie lub parowanie, co umożliwia precyzyjne cięcie i grawerowanie.
Zastosowanie: Plotery laserowe są używane głównie do cięcia i grawerowania materiałów takich jak drewno, akryl, skóra, tworzywa sztuczne, a także do cięcia metali (np. stali nierdzewnej, aluminium). Są szeroko wykorzystywane w przemyśle reklamowym, motoryzacyjnym, meblarskim, jubilerskim, a także w produkcji prototypów i elementów dekoracyjnych.
Zalety: Plotery laserowe zapewniają dużą precyzję cięcia, małą szerokość cięcia (tzw. "struga"), co pozwala na uzyskiwanie bardzo szczegółowych kształtów, bez potrzeby dalszego wykańczania krawędzi. W porównaniu do tradycyjnych metod cięcia, plotery laserowe umożliwiają uzyskanie lepszej jakości powierzchni i większej szybkości obróbki.
6. Sterowanie w Obrabiarkach CNC
-
Podstawy Sterowania CNC
- Sterowanie obrabiarkami CNC odbywa się za pomocą systemów komputerowych, które precyzyjnie kontrolują ruchy maszyn, umożliwiając obróbkę detali z dużą dokładnością i powtarzalnością. Jednym z kluczowych elementów sterowania w obrabiarkach CNC jest system G-code (kod G), który umożliwia komunikację między komputerem sterującym a maszyną.
-
Sterowanie Ruchem Osi – G-code
-
G-code to zestaw poleceń, które określają ruchy maszyn oraz inne parametry procesu obróbki.
Oto podstawowe komendy wykorzystywane w G-code:
G00 – Ruch szybki (szybki ruch narzędzia do określonej pozycji).
G01 – Ruch liniowy z określoną prędkością skrawania (np. frezowanie, toczenie).
G02 – Ruch po łuku w kierunku zgodnym z ruchem wskazówek zegara (frezowanie).
G03 – Ruch po łuku w kierunku przeciwnym do ruchu wskazówek zegara (frezowanie).
G04 – Pauza (opóźnienie na określony czas).
G17 – Wybór płaszczyzny XY (dla operacji obróbczych w tej płaszczyźnie).
G18 – Wybór płaszczyzny ZX.
G19 – Wybór płaszczyzny YZ.
G20 – Ustawienie jednostek w calach (w systemach metrycznych jest to G21).
G21 – Ustawienie jednostek w milimetrach.
G28 – Przesunięcie narzędzia do pozycji referencyjnej.
G30 – Przesunięcie narzędzia do drugiej pozycji referencyjnej.
G40 – Wyłączenie kompensacji promienia narzędzia.
G41 – Kompensacja promienia narzędzia w lewo (w stosunku do ścieżki).
G42 – Kompensacja promienia narzędzia w prawo.
G43 – Włączenie kompensacji długości narzędzia.
G44 – Włączenie kompensacji długości narzędzia w przeciwnym kierunku.
G53 – Użycie układu współrzędnych maszyny (bez korekt).
G54-G59 – Wybór układu współrzędnych roboczych (możliwość ustawienia różnych układów współrzędnych).
G70 – Cykl powtórzeń obróbczych (np. w toczeniu).
G73 – Cykl wiercenia o głębokości (np. wiertło).
G81 – Cykl wiercenia (operacja wiercenia na określoną głębokość).
G82 – Cykl wiercenia z pauzą (wiercenie z zatrzymaniem narzędzia).
G83 – Cykl wiercenia głębokiego.
G90 – Programowanie w trybie absolutnym (współrzędne odnoszące się do punktu zerowego).
G91 – Programowanie w trybie inkrementalnym (współrzędne odnoszące się do ostatniej pozycji).
G92 – Ustawienie zerowej pozycji.
G94 – Ustawienie jednostek prędkości skrawania (np. mm/min).
G95 – Ustawienie jednostek prędkości obrotowej (np. obr/min).
G98 – Powrót narzędzia do pozycji startowej (po zakończeniu cyklu wiercenia).
G99 – Powrót narzędzia do pozycji początkowej.
-
Programowanie CAM – Integracja Projektowania z Produkcją
-
Programowanie CAM (Computer-Aided Manufacturing) łączy procesy projektowania (CAD) z
produkcją, umożliwiając wygenerowanie precyzyjnych instrukcji dla obrabiarek CNC.
Oprogramowanie CAM pozwala na:
Generowanie ścieżek narzędziowych, które uwzględniają geometrię obrabianego detalu, materiał, narzędzie i parametry obróbcze.
Optymalizację procesu produkcyjnego, m.in. poprzez automatyczne dostosowanie prędkości i głębokości skrawania do konkretnego zadania.
Popularne programy CAM to Mastercam, Fusion360, VisualMill, które umożliwiają tworzenie
dokładnych i wydajnych programów obróbczych.
-
Typowe Kontrolery CNC
-
Kontrolery CNC to systemy komputerowe, które sterują ruchem maszyny i realizują programy
G-code. Wyróżnia się kilka typów kontrolerów, z których każdy ma swoje specyficzne
właściwości:
Fanuc: Japoński system, który stanowi jeden z najczęściej używanych standardów w przemyśle. Fanuc jest ceniony za wysoką niezawodność i wszechstronność, a także łatwość integracji z różnymi maszynami. Jest popularny w przemyśle motoryzacyjnym, elektronicznym i w produkcji precyzyjnej.
Siemens Sinumerik: Zaawansowany system sterowania o rozbudowanej funkcjonalności. Sinumerik oferuje wszechstronne możliwości programowania, w tym obróbkę wieloosiową oraz precyzyjne kontrolowanie procesów technologicznych. Jest często wykorzystywany w skomplikowanej produkcji, np. w przemyśle lotniczym i medycznym.
Heidenhain: Popularny w produkcji precyzyjnej, zwłaszcza w branży narzędziowej i wytwarzania form. Heidenhain oferuje zaawansowane funkcje pomiarowe i monitorowanie jakości procesu produkcji. Jest ceniony w branżach, które wymagają dużej precyzji, takich jak produkcja form wtryskowych, obróbka detali o bardzo małych tolerancjach.
-
Symulacje i Testy Przed Uruchomieniem
-
Przed uruchomieniem programu obróbczego na rzeczywistej maszynie, niezbędne jest testowanie
programu. Wykorzystanie oprogramowania symulacyjnego pozwala na:
Sprawdzanie błędów w ścieżkach narzędziowych, takich jak kolizje narzędzi z detalem lub z elementami maszyny.
Optymalizację procesu, np. poprzez testowanie różnych strategii skrawania i prędkości obróbczych.
VisualMill – oprogramowanie do symulacji obróbki CNC, szczególnie przydatne w frezowaniu.
Fusion360 – oferuje pełne wsparcie w zakresie CAM i umożliwia symulację procesów obróbczych w 3D.
Mastercam – oprogramowanie CAM o szerokim zakresie funkcji, w tym symulacja wieloosiowej obróbki.
Przykłady popularnych programów do symulacji to: -
Diagnostyka i Błędy w Sterowaniu
-
Podczas pracy obrabiarki CNC mogą wystąpić różne problemy, które wymagają szybkiej diagnozy
i naprawy. Typowe błędy programowe to np. nieprawidłowe współrzędne, które mogą prowadzić do
kolizji narzędzi lub braku wykonania zaplanowanych operacji.
"Axis Overload": Alarm informujący o przeciążeniu osi. Może być spowodowany zbyt dużym naciskiem na narzędzie lub zbyt dużą prędkością ruchu. Rozwiązaniem może być zmniejszenie prędkości skrawania lub dostosowanie parametrów maszyny.
Błędy w synchronizacji osi: Może to prowadzić do błędów w geometrii obróbki. W takim przypadku, rozwiązaniem może być kalibracja i ponowne ustawienie maszyn, aby poprawić dokładność.
Przykłady alarmów i ich rozwiązań: -
Kalibracja Maszyn
-
Kalibracja maszyn CNC jest procesem, który zapewnia, że maszyna działa zgodnie z wymaganiami
dokładności i precyzji. Może obejmować:
Sprawdzanie i ustawienie zerowych punktów osi.
Kalibracja układów pomiarowych i czujników.
Weryfikacja i korekcja błędów geometrii narzędzi, które mogą wpływać na dokładność obróbki.
Regularna kalibracja jest kluczowa w utrzymaniu jakości produkcji, szczególnie w procesach wymagających dużej precyzji.
7. Odmiany Konstrukcyjne Obrabiarek CNC
-
Podział według Przeznaczenia
Obrabiarki uniwersalne są przeznaczone do szerokiego zakresu operacji skrawania, takich jak frezowanie, toczenie czy wiercenie. Możliwość łatwego przystosowania do różnych zadań sprawia, że są one popularne w warsztatach, gdzie wymagane jest częste zmienianie zadań i obróbka różnorodnych materiałów.
Obrabiarki specjalistyczne to maszyny dedykowane do konkretnego rodzaju obróbki, często zaprojektowane z myślą o masowej produkcji określonych detali. Na przykład, obrabiarki transferowe w produkcji wielkoseryjnej wykorzystują automatyczne systemy przenoszenia detali z jednej strefy obróbczej do drugiej, co znacznie zwiększa efektywność.
-
Podział według Konfiguracji Osi
3-osiowe: Maszyny 3-osiowe są standardem w obrabiarkach CNC. Posiadają trzy podstawowe osie: X, Y, Z (ruchy w poziomie, wzdłuż osi poziomej i pionowej). Umożliwiają one precyzyjne wykonywanie podstawowych operacji, takich jak frezowanie czy wiercenie. Stosowane w produkcji detalicznej, gdzie kształty nie są zbyt skomplikowane.
5-osiowe: Obrabiarki 5-osiowe są w stanie obrabiać skomplikowane kształty, dzięki większej liczbie osi ruchu. Mają 3 osie robocze (X, Y, Z) oraz 2 osie dodatkowe (często A i B), które pozwalają na obrót detalu wokół tych osi. Produkcja turbin lotniczych to jeden z przykładów zastosowania obrabiarek 5-osiowych, gdzie precyzyjna obróbka złożonych detali jest niezbędna.
-
Podział według Sposobu Montażu Narzędzia i Przedmiotu Obrabianego
-
Maszyny Portalowe: Charakteryzują się dużą stabilnością i sztywnością,
dzięki konstrukcji, gdzie główny stół roboczy znajduje się w centrum maszyny, a głowica
narzędziowa porusza się po portalach. Są szczególnie efektywne przy obróbce dużych detali o
złożonych kształtach.
Maszyny pionowe (np. Haas VF-2) posiadają wrzeciono umieszczone w pionie, co sprawia, że są wygodne w obróbce detali, które wymagają szybkiego dostępu do powierzchni roboczej. Są to często centra obróbcze wykorzystywane do frezowania.
Maszyny poziome (np. Mazak HCN-5000) mają wrzeciono ustawione poziomo, co zapewnia lepszą wydajność przy obróbce detali o większej objętości i przy dużych seriach produkcyjnych. Takie maszyny umożliwiają lepsze wykorzystanie przestrzeni roboczej i większą precyzję obróbki w poziomie.
-
Centra Obróbcze i Ich Funkcje
- Centra obróbcze CNC to zaawansowane maszyny, które łączą funkcje frezowania, wiercenia, toczenia i innych operacji skrawających w jednym urządzeniu. Dzięki dużej liczbie osi, możliwością programowania i wysokiej precyzji, centra obróbcze stanowią fundament w produkcji precyzyjnej w takich branżach jak lotnictwo, motoryzacja, przemysł medyczny czy elektroniczny.
-
Rozwój i Przyszłość Obrabiarek CNC
Robotyzacja i Automatyzacja: W przyszłości obrabiarki CNC będą coraz bardziej zintegrowane z systemami robotycznymi, które automatycznie będą przenosić materiały i detale, wymieniać narzędzia, a także kontrolować jakość produktów. Tego typu rozwiązania zminimalizują błędy ludzkie, przyspieszą procesy produkcyjne i poprawią wydajność.
Inteligentne Maszyny z Sztuczną Inteligencją (AI): Sztuczna inteligencja ma szansę zrewolucjonizować przemysł CNC, umożliwiając maszynom samodzielne dostosowanie parametrów obróbczych w zależności od analizowanych danych. Takie systemy będą w stanie przewidywać i rozwiązywać problemy, takie jak zużycie narzędzi czy zmieniające się właściwości materiałów.
Trendy w Materiałach Konstrukcyjnych: W przyszłości, do konstrukcji obrabiarek, coraz częściej będą wykorzystywane kompozytowe materiały, które łączą lekkie, ale sztywne właściwości. Takie materiały pozwolą na zmniejszenie wagi maszyn, co może zwiększyć ich prędkość obróbki, a jednocześnie utrzymać wysoką precyzję.
8. Podsumowanie
Obrabiarki CNC (Computer Numerical Control) to maszyny wyposażone w systemy komputerowe,
które
umożliwiają precyzyjną i zautomatyzowaną obróbkę materiałów. Technologia CNC rozwinęła się od lat
50. XX
wieku, przekształcając produkcję w wielu branżach, takich jak lotnictwo, motoryzacja czy elektronika.
Obrabiarki CNC dzielą się na uniwersalne i specjalistyczne, a ich konfiguracja osi (zwykle 3 do 5
osi)
oraz sposób montażu (portalowe, pionowe, poziome) decydują o ich zastosowaniu. Maszyny te są sterowane
za pomocą kodów G i programów CAM, co pozwala na dużą precyzję i optymalizację produkcji. W przyszłości,
obrabiarki będą coraz bardziej zautomatyzowane i zintegrowane z robotami przemysłowymi, a sztuczna
inteligencja pomoże w dalszym rozwoju ich wydajności.